GGBS (Ground granulated blast furnace slag)
"Magic Durabuild Material Pvt Ltd (Formerly known as SR Group - Highway Supplies and Network Pvt Ltd) continues to provide the same trusted service across our entire product range. You can rely on our expertise."
Environment friendly, Supplementary Cementitious material to provide long term strength, Durability & cost saving.
Ground granulated blast furnace slag (GGBS) is a hydraulic binder, i.e. cement, which has proven itself reliably and used all over the world since the mid 1800s. GGBS is a by product of steel & it is used as a Cement substitute without compromising on quality of concrete.
Thirty-eight years after the patent for Portland cement was first lodged by John Aspdin in 1824, Emil Langin discovered GGBS cement. By 1865, commercial production of lime activated GGBS had commenced in Germany and by 1880 GGBS was being used with Portland cement as the activator. In 1889 it was used for construction of the Paris Metro. The United States commenced production of slag cements in 1896. Since then Europe, with its many blast furnaces and steel industries has used GGBS extensively in all manner of structures. By 1914, GGBS was being manufactured in Scotland. BS 146 was published in 1923 followed by BS 6699 in 1986 for GGBS. It improves the durability of concrete, and its production is virtually CO2-free. Yet its many advantages in producing sustainable, high-quality concrete remain underappreciated and underused. In an increasingly resource-constrained and environmentally conscious world, all that is about to change.
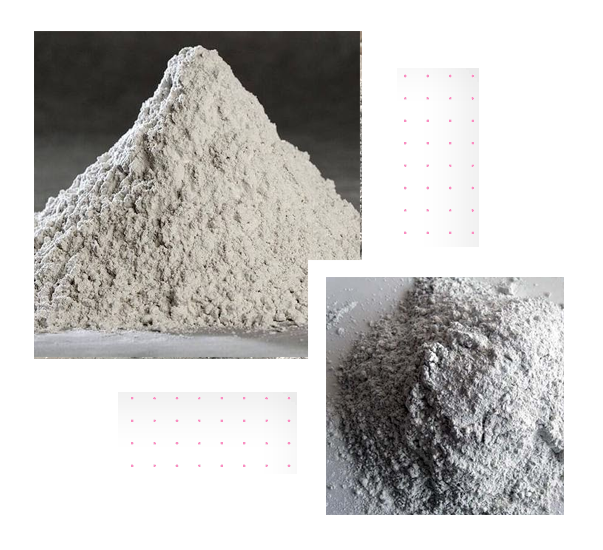
Blast furnaces produce pig iron, together with a slag by-product: a tightly controlled and stable material with the same constituents, though in different proportions, to normal cement. If the slag is vitrified by rapid quenching as it comes from the blast furnace, its cementitious qualities are preserved. Dried and ground to a fine powder, GGBS can be used to make durable concrete. To ensure its activation, GGBS is most often used with ordinary Portland cement. It will typically replace 25 – 70% of cement on an equal weight basis.
- SILICA 27 – 32
- LIME 30 – 40
- ALUMINA 17 – 31
- IRON 0 – 1
- MAGNESIA 0 – 17
- GLASS CONTENT 85% MIN.
- Dispersion of Cement Particles
- Particle Packing Effect
- Secondary Reaction
- IRON 0 – 1
- Long term Strength development
- Improves Ultimate & Flexural
- Strength of Concrete
- Max. Reduction in heat of hydration.
- High Impermeability.
- Resistance to Chemical Attacks
Concrete should be a friend of the environment in all stages of its life span, from raw material production to demolition, making it a natural choice for sustainable home construction. Here are some of the reasons why concrete made out of GGBS will add sustainability.
Resource efficiency: Huge savings in lime stone utilisation leads to conservation of natural resources for future generation.
Durability: GGBS Concrete builds durable, long-lasting structures that will not rust, rot, or burn. Life spans for concrete building products can be double or triple those of other common building materials.
Thermal mass: Structures built with GGBS concrete walls, foundations, and floors are highly energy efficient because they take advantage of concretes inherent thermal massor ability to absorb and retain heat.
Reflectivity: GGBS Concrete (Light coloured) minimizes the effects that produce urban heat islands.
Minimal waste: GGBS Concrete can be produced in the quantities needed for each project, reducing waste. After a concrete structure has served its original purpose, the concrete can be crushed and recycled into aggregate for use in new concrete pavements or as backfill or road base.